Какие запчасти для авто можно сделать на 3D-принтере
Автомобиль – это всегда затратно. Особенно когда речь заходит о ремонте или поиске запчастей. Если машина новая, нужная деталь легко найдется на авторазборке или в интернет-магазине. Но что делать, если автомобиль достаточно старый и запчастей на него почти не осталось? Либо деталь идет в комплекте с другими механизмами в составе узла и стоит бешеных денег? Во всех этих случаях стоит обратить свое внимание на технологию 3D-печати.
Как используется 3Д-печать автозапчастей?
Говоря о сферах использования 3D-печати автозапчастей , можно рассмотреть несколько интересных отраслей. Начнем по порядку, от крупногабаритных элементов до деталей попроще:
- Элементы кузова для сборки нового силуэта авто. Такие проекты тоже есть. Их реализуют умельцы-одиночки или частные компании. Они печатают небольшие кусочки дверей, капота, крыльев и прочих деталей, которые потом склеивают воедино. Возможно, с увеличением размеров печатной площади принтера и появлением новых материалов мы увидим в будущем полностью напечатанный кузов без склеек.
- Детали для тюнинга в автомобильных ателье. Разные обвесы, которые дают машине новый облик, сохраняя черты старого кузова. Также они могут влиять на аэродинамику авто.
- Элементы интерьера. Это могут быть как взаимозаменяемые компоненты, так и детали, которые выдумал и напечатал сам хозяин авто. Такая печать будет интересна реставрационным мастерским, частным СТО или простым автомобилистам, которые хотят облагородить салон своего автомобиля.
- Небольшие элементы из пластика, которые являются частью одного узла. Например, у машины стерлась пластиковая заглушка или шестерня в тормозном блоке. В сборе данный узел обойдется в 15 000 рублей. Магазин не станет разбирать весь блок, чтобы продать одну маленькую деталь. Тут и придет на помощь 3D-печать. Отличная идея для частной мастерской или СТО.
- Заглушки для дисков. Это одна из самых востребованных деталей. Порой ее проще распечатать и покрасить, чем искать на разборке или заказывать в интернете. К тому же заглушку можно стилизовать по собственному вкусу. Неплохая товарная позиция для магазинов по продаже литья и шин, шиномонтажек, а также частных мастерских.
- Фары. Новая оптика всегда выигрышно смотрится. Головной свет вовсе может изменить облик авто. Подобную услугу могут оказывать частные мастерские и профильные СТО. В данной статье мы покажем, как делают основу под фары. Ниже, в отдельном кейсе.
- Бампер. Данную часть автомобиля можно смело назвать расходником. Бампер принимает на себя все удары, а также является самой окрашиваемой запчастью в СТО. Его проще напечатать на принтере, чем ждать с разборки или тем более покупать новый. Такую позицию в прайсе выгодно иметь мастерским, которые занимаются кузовным ремонтом.
- Как отдельный вариант применения можно выделить область проектирования и инжиниринга, когда детали или узлы создают в заданном масштабе с помощью технологий 3D-печати.
Вообще, область 3D-печати для автомобиля ограничена только эксплуатационными характеристиками детали, а также фантазией автовладельца. Более подробные примеры печати смотрите ниже в статье.
Интересно! Передняя фара для BMW X5 обойдется автовладельцу в 22 000–23 000 рублей. Если в ней сломаются пластиковые заглушки, то придется покупать оптику в сборе, либо напечатать элемент на 3D-принтере. Такой ремонт обойдется в среднем в 30–40 раз дешевле, чем покупка новой фары.
Какие технологии 3D-печати для этого подойдут?
Разные принтеры предназначены для решения тех или иных задач. Рассмотрим на конкретных примерах:
- Печать запчастей нужна для того, чтобы сделать какой-то грандиозный проект. Например, воссоздать кузов ретромобиля. Для этих целей лучше рассматривать принтеры с большой рабочей камерой для печати. Так как детали так или иначе будут проходить постобработку (грунтование, покраска), высокая точность не понадобится. Для этих целей подойдет технология FDM /FFF (метод спекание пластика слой за слоем). Конечные детали будут стоить недорого, да и овладеть подобным принтером сможет даже новичок. Более продвинутый уровень – SLS и SLM . Детали будут печататься под действием спекания металлизированного порошка. Это дороже, чем пластик, но и прочнее.
- Печать деталей для внешнего тюнинга. Если нужно сделать обвес, накладку на порог или антикрыло, которое потом все равно придется грунтовать и красить, то проще и дешевле использовать FDM/FFF-принтеры. Размер области печати зависит только от самих деталей. Например, если мастерская печатает только колпачки для дисков, то для нее подойдут самые простые принтеры небольших габаритов. Для производства длинных накладок, обвесов и спойлеров нужны более крупные принтеры.
- Подвижные элементы узлов (шестерни, рычажки и прочие). Для изготовления этих деталей потребуется высокая точность печати. В противном случае вы можете испортить узел. Лучше отдать предпочтение технологии фотополимерной печати (DLP/SLA/SLS).
- Компоненты интерьера. Заглушки, ободки датчиков, дверные ручки, кнопки, рычаги КПП – все то, за что цепляется глаз. Для таких деталей нужна точность и минимальная постобработка. В этом случае можно также отдать предпочтение DLP/SLA, так как себестоимость небольших деталей в любом случае будет меньше, чем цена аналогов в магазине.
Естественно, на выбор конечной технологии влияют финансовые возможности человека или СТО. А также уровень навыка печати на том или ином принтере. Однако в большинстве случаев для печати деталей хватит простого FDM-принтера.
Информация! В 2020 году среди самых крупных FDM-устройств можно выделить CreatBot D600. Его рабочая камера имеет габариты 600 мм по каждой из осей. Правда, стоит такой принтер, как новая бюджетная легковушка. Его цена переваливает за отметку 780 000 рублей.
Материалы для 3D-печати запчастей
Стоит сразу же сделать оговорку: технология печати запчастей для автомобиля выгодна в том случае, если используются относительно недорогие и прочные материалы. Если вы собираетесь делать запчасть из дорого пластика или полимера, лучше просто купить оригинальную деталь в магазине.
Важно! Юридический вопрос использования деталей, напечатанных на 3D-принтере, до сих пор не решен. В частности, лучше не использовать оригинальные эскизы трехмерных моделей, на которых есть фирменный знак или логотип бренда. Например: Toyota, BMW, Ford и прочие. Так вы не нарушите права компаний на интеллектуальную собственность. Также могут появиться вопросы у ГИБДД, если вы установите себе на машину нестандартизированное антикрыло либо другой обвес.
Рассмотрим материалы в зависимости от типа используемого принтера:
- FDM/FFF: печать при помощи недорогих ABS , PLA или Nylon-пластиков;
- DLP/SLA/SLS: использование недорогих и прочных фотополимеров (смол).
Для печати деталей, которые будут установлены в подкапотное пространство, лучше использовать Nylon. Он держит высокую температуру и обладает хорошей прочностью. Для внешнего тюнинга, а также части внутренней отделки можно смело брать ABS или PLA. Если нужно сделать эмблему, ровную ручку или другую аккуратную деталь, стоит обратить внимание на фотополимеры.
Выбор конкретного пластика, нейлона или смолы будет зависеть от используемого принтера. Какие-то модели работают только на оригинальных расходных материалах, другие способны «переварить» расходники от любого производителя. Ниже мы опишем пару кейсов с примерами работ, где будет указан тип материала.
Факт! Немецкий производитель больших промышленных 3D-принтеров сделал электробайк, где 80 % компонентов были изготовлены методом печати FFF. Для этих целей задействовали много материалов, включая фирменный пластик BigRep PLA.
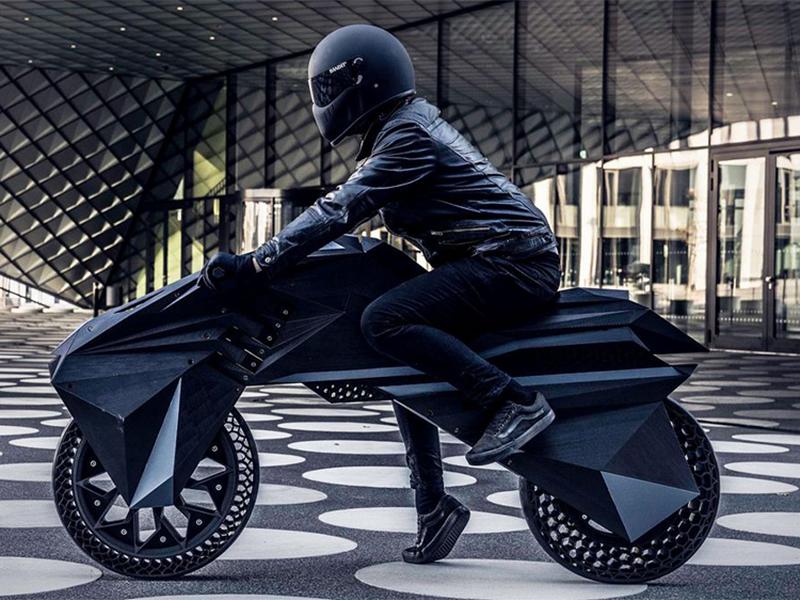
Примеры печати автозапчастей на 3D-принтере
Здесь собраны примеры работ, которые можно разделить на три большие категории:
Внешние детали: кузовные запчасти, компоненты дисков, обвесы.
Детали интерьера: заглушки, ручки, накладки и проч.
Конечно, это не все способы применения. Практически любую запчасть, которая сделана из пластика или подобного материала, можно воплотить на 3D-принтере. Главное, нарисовать точный трехмерный CAD-проект. Его можно найти в интернете как готовый файл либо воспользоваться 3D-сканером и снять «виртуальный слепок» вручную.
Информация! Для создания элементов внешнего обвеса стоит сделать полную трехмерную модель кузова специальным сканером. Так вы точно учтете все дефекты по дверям, бамперам, крыльям и прочим деталям. Полученный обвес встанет точно, без зазоров. Его не нужно будет перепечатывать или «дорабатывать напильником».
Бампер на 3D-принтере
Перейдем к непосредственному рассмотрению кейсов пользователей. Начнем с объемного проекта – печати части бампера для автомобиля VW Touareg. Это довольно большая запчасть. Ее не получится сделать в один проход. Поэтому приходится печать кусочками, после чего склеивать полученные запчасти воедино.
Выгода! Бампер на VW Touareg в хорошем состоянии обойдется автомобилисту в 8 500–15 000 рублей. Цена зависит от состояния запчасти. Методом 3D-печати данную деталь можно сделать за 20–30 % от данной стоимости.
В этом проекте использовали PLA, так как обычный ABS не дал нужного результата. Для изготовления модели бампера задействовали программу Netfabb. Так удалось достичь минимума поддержек. Это спасло от последующей массовой резки. Сама печать велась с OctoPront на принтере Ultimaker 2 Extended+.
На фотографиях видно, что в процессе задействован белый и цветной пластик. Компоненты склеивались между собой дихлорметаном (ДХМ). Он лучше держит две детали между собой и не так токсичен, как дихлорэтан. Но работать все равно лучше в респираторе. Швы заделаны тем же PLA-прутком с помощью цифрового паяльника. Но сам печатник отметил, что лучше использовать 3D-ручку.
Проект по этапам:
Пользователь указал, что печатал форму для изготовления заготовки под бампер. То есть это была болванка. Но по факту данную деталь можно было бы использовать и в качестве основной. Если ее качественно загрунтовать и покрасить, то различия сведутся к минимуму.
Фара на 3D-принтере
Второй кейс – изготовление заготовки под переднюю оптику для реплики автомобиля Audi R8. Данная болванка была сделана специально для отливки конечного изделия из жидкого пластика. За основу была взята 3D-модель, которую пользователь вытащил из CAD-файла кузова R8.
Для изготовления болванки взяли 3D-принтер Prusa i3 с рабочей поверхностью 200 на 200 мм. Трехмерную деталь предварительно конвертировали в формат STL для удобства печати. Программа для разбивки проекта по частям – Netfabb Basic.
Сам пользователь отметил, что можно было использовать другие приложения с возможностью выставления стыковочных фасок. Но именно в этом проекте болванку распечатывали по частям «как есть». После чего склеивали суперклеем. Для работы был взят синий PLA.
Результат работ впечатляет. Многие автомобилисты в комментариях отметили, что саму болванку можно было использовать как пластиковую основу под установку галогеновых лампочек или иной оптики. Впрочем, такие изделия тоже можно увидеть на просторах интернета.
Информация! Отдельные 3D-элементы или полноценные узлы в сборке можно посмотреть на сайтах: Pinshape, Turbosquid, Thingiverse, Free3d.
Трехмерная печать уже нашла свое применение в изготовлении деталей и запасных частей для автомобилей. Ее используют тюнинговые ателье, профильные СТО или частные мастера. На принтере можно сделать практически любую деталь-аналог, которую можно использовать как пластиковую запчасть. Ограничения в основном касаются только температурного режима использования. Для внешних обвесов и крупных деталей «под покрас» подходят FDM/FFF-принтеры. Для изготовления более точных и аккуратных элементов, лучше взять DLP/SLA/SLS-аппарат.
- 24 мая 2020
- 6712
Автомобили, напечатанные на принтере
24 сентября 2019
О 3D-принтерах сегодня слышали даже те, кто бесконечно далек от IT-индустрии, но для гиков эти устройства уже стали обыденностью, поскольку “первая волна” массового распространения 3D-принтеров произошла еще в 2014-2015 годах. Да, какое-то время эта технология была доступна лишь в B2B-сегменте и на государственных предприятиях, но уже в 2016 рынок наводнили модели стоимостью менее 1000$, что позволило обычным людям реализовать многие (зачастую довольно сумасшедшие) идеи, копившиеся в их головах с момента появления первых новостей о 3D-принтерах. В результате, к сегодняшнему дню в Интернете можно без проблем скачать адаптированную для печати модельку, а в новостных сводках то и дело проскакивают известия о различных достижениях в печати вещей, которые еще недавно можно было купить только в магазине. Сегодня речь пойдет о “напечатанных” автомобилях, до сих кажущихся чем-то фантастическим, хотя на самом деле, печатать машины стали еще с момента появления первых потребительских 3D-принтеров — то есть, 4-5 лет назад.
С другой стороны, еще в конце нулевых нельзя было и мечтать о возможности печати полноценных транспортных средств, не отличающихся от своих привычных собратьев и 2019 стал переломным годом в этом вопросе: к примеру, начало сентября ознаменовалось новостью о первом самоуправляемом автобусе, созданном, в основном, при помощи 3D-принтера.
Olli
Проект стартовал в 2016, когда малоизвестная компания Local Motors совместно с компьютерным гигантом IBM выпустила небольшой самоуправляемый автобус Olli. В отличие от оригинала, обновленная модель была произведена, по большей части, на 3D-принтере, технические характеристики улучшились, неизменными остались только ИИ-наработки IBM, обеспечивающие реализацию автопилота 4 уровня.
Мини-автобус может проехать на одном заряде до 160 км, вмещает 12 человек и развивает скорость до 40 км/ч. Конечно, Olli не является общественном транспортом в обычном понимании этого слова, но зато уже сейчас он может служить в качестве шаттла для перевозки пассажиров по территории парков отдыха, военных баз, университетских кампусов, студгородков, аэропортов, и прочих закрытых зон с низким скоростным режимом.
Lamborghini Aventador
В июле этого года много шума наделала необычная история: американский ученый Стерлинг Бакус вместе со своим 11-летним сыном завершили работу над полноразмерной копией суперкара Lamborghini Aventador. Все производство и сборка проходили в обычном гараже, а оборудование было куплено на eBay. Если конкретнее, первым делом Бакусы приобрели три принтера CR-10S, CR105S и QIDI Xpro, после чего скачали все необходимые модели из Интернета. Первые 2 принтера использовались для печати пластиковых деталей, последний – для создания частей из более прочных материалов, недостающие детали были также куплены на eBay.
Стоит отметить, что многие компоненты не потребовали значительных финансовых вложений – например, передние и задние фары выполнены из пластика ASA, ABS и PETG, который можно купить в любом магазине электроники. Рама автомобиля также обошлась относительно недорого, так как ее напечатали из обычной стали, что к тому же увеличило прочность и безопасность конструкции.
В общей сложности на проект ушло около 20 000 долларов, при этом настоящая Lamborghini Aventador стоит 300$ тысяч или 20 миллионов рублей. Весь процесс постройки занял полтора года.
Помимо фанатских напечатанных автомобилей, все распространено применение 3D-принтеров известными автоконцернами для восстановления культовых, но давно исчезнувших моделей, для которых уже практически не осталось комплектующих. Так, наиболее примечательны проекты по реставрации BMW 507 и Audi Type C.
Audi Type C
Audi Type C Replica является копией одноименного спорткара представленного в 1936 году. Работа над новым автомобилем стартовала в 2015 и стала дебютным проектом Audi на ниве 3D-печати. Таким образом автопроизводитель стремился продемонстрировать широкой публике впечатляющий потенциал печати металлических деталей.
Это стремление было продиктовано использованием SLS-принтера, позволившего напечатать абсолютно все металлические части автомобиля и затем вручную собрать их воедино.
BMW 507
В случае с BMW 507 все началось куда забавнее: эту машину обнаружили в заброшенном гараже на бывшем ранчо самого Элвиса Пресли, после чего фанаты певца и любители классических автомобилей стали упрашивать BMW восстановить 507-ю. В итоге работа заняла целых два года, поскольку с момента выпуска оригинальной BMW 507 в 1957 г. не осталось ни одной “живой” детали просто потому, что эта модель была произведена ограниченным тиражом в 252 штуки.
Но с помощью архивных CAD-моделей баварцам удалось напечатать все отсутствующие детали, среди которых были дверные ручки, оконные стекла и элементы интерьера. В 2016 родстер был полностью отреставрирован и в том же году BMW 507 показали на автомобильном фестивале в Пеббл-Бич.
В то же время, некоторые производители строят планы по серийному выпуску автомобилей с помощью 3D-печати. Причины данных намерений очевидны: во-первых, это ускорение и удешевление производства, а во-вторых, на принтере возможно достичь некоторых конструктивных преимуществ, не доступных при обычных технологиях автомобилестроения.
Toyota uBox
Одной из первых компаний, “обкатывающих” 3D-принтеры в серийном производстве стала японская Toyota, разработавшая концепт uBox. В его создании принимал участие Международный центр исследований в области автомобильных технологий Университета Клемсона (Южная Каролина). Главная особенность uBox заключается в том, что модульный интерьер и вся электронная начинка распечатаны на 3D-принтере (внешние детали и рама по-прежнему изготавливаются при помощи традиционных технологий.
По словам Toyota, главная идея этого автомобиля – наличие возможности максимальной кастомизации интерьера. Возможно, именно поэтому японцы позиционируют его, как “персонализируемую машину будущего для поколения Z”. Toyota уже заявила о планах по созданию специального онлайн ресурса для владельцев uBox, где они смогут делиться вариантами дизайна дверных накладок, приборной панели, вентиляционных отверстий и пр.
Это сделано для того, чтобы пользователи могли распечатать необходимый элемент у себя дома и самостоятельно установить его, не обращаясь к дилеру или СТО. Помимо прочего, uBox имеет абсолютно ровный пол в салоне, чтобы у владельца автомобиля была возможность располагать пассажирские сидения по своему усмотрению.
Bentley EXP 10 Speed 6
3D-печать не оставил без внимания даже такой люксовый производитель как Bentley. Глава компании Вольфганг Дюрхаймер пообещал, что концепт Bentley EXP 10 Speed 6 поступит в продажу до 2020. Практически все металлические элементы конструкции этого автомобиля будут напечатаны на 3D-принтере, но особое внимание инженеры уделяют решетке радиатора со сложным объемным рисунком вместо привычной для Bentley плоской радиаторной решетки.
The Blade
Этот автомобиль принято считать “первым в мире напечатанным суперкаром”. Корпус The Blade выполнен из углеволокна, а внутри него находится множество алюминиевых трубок – все это прикреплено к шасси автомобиля для снижения веса и увеличения безопасности. За разработку The Blade ответственна компания Divergent3D, одной из главных целей которой является продвижение инновационных технологий автопрома, делающих автомобили более легкими, а их производство – экономичнее.
EDAG Light Cocoon
EDAG Group – это один из крупнейших независимых разработчиков в автомобильной индустрии. Данная организация занимается упрощением и оптимизацией технологий производства автомобилей, и главная предназначение концепта Light Cocoon аналогична вышеупомянутому The Blade – а именно, доказать возможность создания более легких ТС, без увеличения расходов на производство и сборку компонентов.
Строение корпуса EDAG Light Cocoon похоже на лист: панели имеют пористую структуру для обеспечения низкого веса, а чтобы оставить безопасность автомобиля на прежнем уровне, корпусные панели пронизаны тонкими нитями прочной сверхлегкой ткани Jack Wolfskin. Помимо того, что пористая структура более удобна именно для 3D-печати, она позволяет осуществлять различные световые эффекты для демонстрации “скелетообразного” строения автомобиля.
Источник https://vektorus.ru/blog/3d-pechat-avtozapchastej.html
Источник https://www.computerra.ru/241280/avtomobili-napechatannye-na-printere/