Техническое обслуживание электрооборудования автомобиля
1. Техническое обслуживание аккумуляторной батареи
Основные неисправности аккумуляторной батареи: разряд и саморазряд, короткое замыкание пластин при выпадении активной массы. Кроме того, в результате понижения уровня электролита, а также длительного хранения аккумулятора без подзарядки возможна сульфитация пластин, хотя вероятность ее в современных конструкциях батарей при нормальном уровне электролита значительно снижена. Выпадение активной массы приводит также к понижению емкости батареи. При эксплуатации возникают трещины стенок батареи, происходит снижение уровня электролита и его плотности.
При пониженном уровне электролита в аккумуляторы батареи доливают дистиллированную воду. Электролит доливают лишь в случае, когда понижение его уровня вызвано утечкой или расплескиванием. Уровень электролита в аккумуляторных батареях проверяют зимой через 10…15 дней, летом в жаркую погоду через 5…6 дней.
Плотность электролита проверяют автомобильным денсиметром. Для умеренного климатического района этот параметр круглый год должен составлять 1,26 г/см 3 . Зарядку аккумуляторной батареи целесообразно производить раз в три месяца током от 1/10 до 1/13 номинальной емкости батареи.
Ресурс батареи в эксплуатации сокращается в 2…2,5 раза при повышении регулируемого напряжения бортовой сети автомобиля выше оптимального на 10…12 %, т. е. зависит от состояния генератора и регулятора напряжения.
В исправной аккумуляторной батарее величина саморазряда не превышает 2% емкости в сутки. Применение загрязненной серной кислоты и воды, содержащей соли и щелочи (недистиллированной), а также попадание внутрь аккумуляторной батареи различных веществ способствуют образованию дополнительных гальванических пар, что приводит к ускоренному саморазряду. Саморазряд аккумуляторной батареи может быть вызван также попаданием на поверхность аккумулятора грязи и электролита и расслоением электролита при длительном бездействии батареи.
Короткое замыкание пластин в аккумуляторе возникает при выпадении из пластин на дно блока активной массы (шлама). Выпадение активной массы приводит также к понижению емкости батареи. В процессе эксплуатации возникают трещины стенок блока, происходит снижение уровня электролита и его плотности.
При понижении уровня электролита доливают дистиллированную воду, так как она испаряется. Плотность электролита проверяют ареометром, помещенным в стеклянную трубку с резиновой грушей для всасывания электролита (рисунок 1).
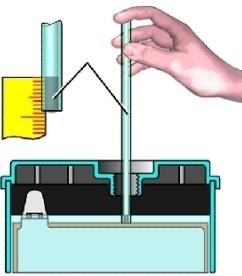

Рисунок 1 – а)-проверка плотности электролита; б)-проверка уровня электролита; в)-нагрузочная вилка
Разница плотности в аккумуляторах батареи не должна превышать 0,01 г/см 3 . Для средней полосы плотность электролита, приведенная к 15°С, для зимы и лета, установлена 1,27 г/см 3 . Уменьшение плотности электролита на 0,01 г/см 3 соответствует разряду аккумуляторной батареи примерно на 6%. Аккумуляторная батарея требует заряда или ремонта, если разряд (хотя бы одного аккумулятора) достигает 50% летом и 25% зимой. После заряда плотность электролита доводят до нормы доливкой дистиллированной воды или электролита плотностью 1,4 г/см 3 . Изменение плотности электролита является одним из основных показателей степени разряда аккумуляторной батареи.
Основные работы технического обслуживания
Аккумуляторные батареи бывают двух видов: необслуживаемые и обслуживаемые (малообслуживаемые).
Необслуживаемые батареи не имеют пробок на аккумуляторах, что исключает возможность доливки в них электролита или дистиллированной воды. Такие батареи не требуют никакого обслуживания в процессе эксплуатации и уход за ними сводится к очистке корпуса и выводов. Чтобы определить уровень электролита на таких АКБ устанавливаются отметки максимума и минимума, а для оценки плотность электролита в него встраивается гидрометр (при полной зарядке индикатор имеет зеленый цвет, при уменьшении заряда его цвет меняется до белого или красного).
Малообслуживаемые батареи требуют чуть большего внимания — периодически необходимо проверять уровень электролита в каждом аккумуляторе (всего их шесть). При понижении уровня, необходимо доливать дистиллированную воду. В редких случаях понижение уровня электролита может быть вызвано утечкой через трещины в корпусе батареи, в этом случае аккумуляторная батарея подлежит утилизации и замене.
Если электрооборудование автомобиля исправно, то такую проверку уровня можно выполнять при сезонном обслуживании (весной и осенью).
Если электрооборудование неисправно (прежде всего на состояние аккумулятора влияет состояние регулятора напряжения и генератора в целом), то до устранения неполадок следует проверять уровень в аккумуляторной батарее не реже одного раза в неделю.
ЕО — перед пуском двигателя проверить общее состояние и крепление АБ. Не допускаются трещины моноблока и крышек, повреждение изоляции проводов или окисление полюсных выводов и клемм, трещины в мастике ее отслоение, сильное загрязнение. О техническом состоянии и степени заряда АБ можно определить по степени накала нитей отдельных включенных ламп, по силе звукового сигнала, по легкости пуска двигателя стартера. В дороге следует следить за показаниями контрольных и сигнальных приборов, характеризующих качество подзаряда АКБ — при загорании красного аварийного сигнала, эксплуатацию следует немедленно прекратить, до устранения причины.
ТО-1 — дополнительно к объему ЕО, провести более тщательно крепежные работы; снять клеммы с выводах штырей, проверить их состояние — окисленные контактные поверхности зачистить мелкозернистой шкуркой или специальными приспособлениями (втулки с мелкими фрезами или металлическими щетками), после чего смазать их техническим вазелином или нанести тонкий слой антиокислительной аэрозоли типа «Унисма». Поверхность АБ следует тщательно очистить, включая вентиляционные отверстия в пробках с последующей продувкой их сжатым воздухом. Пятна белого налета от разлитого электролита легко удаляются ветошью, смоченной в 10% растворе аммиачного спирта. При ТО-1, а в жаркое время года ежедневно, следует проверять уровень электролита в банках АБ. Это делают с помощью уровнемерной трубки, конец которой опускают в наливное отверстие до упора, затем, зажав большим пальцем руки верхний конец трубки, осторожно вынимают и по количеству забранного в трубку электролита (норма 10-15 мм) принимают решение о необходимости доливки в ту или иную банку дистиллированной воды.
ТО-2 — помимо работ, выполняемых при ЕО и ТО-1, в объем работ ТО-2 входят диагностические работы по определению степени разряженности и технического состояния, как АБ в целом, так и отдельных ее элементов. С помощью ареометра с поплавком — денсиметром со шкалой проверяют плотность электролита в каждой банке, характеризующей степень разряженности, а с помощью нагрузочных вилок — напряжение под нагрузкой на выводных полюсах. Проводить эти работы рекомендуется в аккумуляторном цехе, на столе с кислотоупорным покрытием. При необходимости следует выровнять и довести плотность электролита в аккумуляторах до нормы (например, добавлением электролита повышенной плотности). Если же разность плотности превышает 0,02 г/см 3 — АБ необходимо подзарядить в течение 1…2 ч и снова произвести корректировку плотности. Снижение плотности электролита (приведенного к 25°С) на 0,01 г/см 3 свидетельствует о разряженности АБ на 5…6%. Таким образом, если для средней полосы России взята исходная плотность 1,27 г/см 3 , для полностью заряженной батареи, то снижение плотности при замере до 1,23 г/см 3 свидетельствует о разряженности на 25% (предельно допустимая разряженность при зимней эксплуатации), а до 1,19 г/см 3 свидетельствует о разряженности батареи на 50% (предельно допустимая разряженность при летней эксплуатации). Указанные ограничения для зимы связаны с тем, что при низких температурах снижается энергоемкость АБ и пуск двигателя стартером будет крайне затруднен, к тому же электролит с пониженной плотностью склонен к замерзанию и возможно размораживание моноблока АБ, разрушение пластин, сепараторов в т.д. Поэтому, хотя повышенная исходная плотность электролита и сокращает в целом срок службы АБ, в северных широтах ее доводят до 1,30 г/см 3 , а в южных всего лишь до 1,26 г/см 3 . Проверка заряженности АБ аккумуляторными пробниками, при включенных, соответствующих нагрузочных резисторах, должна проводиться при закрытых пробках, не более 5 с — снижение напряжения одного аккумулятора на 0,1 В, свидетельствует о разряженности на 25%.
Таблица 6 — Плотность электролита в полностью заряженной батареи измеренная при температуре +25°С в зависимости от климатической зоны
Автомобильный аккумулятор заряжается специальным зарядным устройством номинальным током, равным 10% от номинальной емкости батареи. Например, при емкости 60 А·ч номинальный ток зарядки должен составлять 6 А.
При этом зарядка может продолжаться до 13…15 часов. Пробки заливных отверстий должны быть обязательно открыты!
Зарядка аккумуляторной батареи считается завершенной, если наблюдается постоянство плотности электролита и выходного напряжения в течение 2-х часов.
Заряд аккумуляторной батареи можно оценить по величине выходного напряжения. Для его измерения необходимо воспользоваться вольтметром или мультиметром, предварительно сняв провод с минусовой клеммы АКБ.
Таблица 7 – Зависимость заряда АКБ от выходного напряжения
Напряжение на выводах, В | Уровень заряда аккумулятора, % |
12,6-12,9 | 100 |
12,3-12,6 | 75 |
12,1-12,3 | 50 |
11,8-12,1 | 25 |
11,5-11,8 | 0 |
Рекомендации по продлению ресурса АКБ:
- Регулярно выполнять техническое обслуживание АКБ.
- Не допускать перезарядки АКБ на автомобиле (напряжение в сети неболее 14,6 В.
- Не допускать недозаряда на автомобиле.
- Следить за натяжением ремня генератора.
- Не перегружать бортовую сеть дополнительными потребителями электроэнергии.
- Не использовать ускоренные методы зарядки АКБ.
- Не допускать попадания в электролит грязи, бензина, масла и т.п.
- Поддерживать в хорошем состоянии системы ДВС, определяющие легкость пуска («заводится с полоборота»).
- Продолжительность одного пуска ДВС (10…15 с), перерыв 1…2 м.
- Заводить ДВС с выключенным сцеплением.
- При температуре ниже -10 0 С перед включением стартера следует предварительно прогреть АКБ путем включения фар на 10…15 мин.
- В зимнее время использовать в ДВС соответствующие марки моторных масел.
- На грузовых автомобилях, где это только возможно, под АКБ следует установить резиновые прокладки.
- Не реже чем через 10-15 дней необходимо проверять степень разряжённости батареи по плотности электролита или нагрузочной вилкой. Батарею, разряжённую более чем на 25% зимой и более чем на 50% летом, следует снять с автомобиля и поставить на подзаряд. В эти же сроки проверяют целостность бака (отсутствие трещин) и просачивание электролита в каждом аккумуляторе батареи.
- Слабо сульфатированные разряженные пластины можно восстановить продолжительными зарядами слабым током (0,03 …0,04 от значения емкости от исходной плотности электролита 1,03 … 1,05 г/см 3 до плотности 1,1 г/см 3 ). Затем слить электролит и цикл повторить, и так несколько раз, пока плотность не перестанет повышаться.
2. Техническое обслуживание автомобильного генератора
Неисправности автомобильного генератора условно делятся на электрические и механические. К электрическим относятся:
- Износ и выход из строя щеток.
- Нарушения контакта или обрыв электрических цепей.
- Короткое замыкание обмоток ротора.
- Поломка регулятора напряжения или диодного моста.
Механические неисправности, как правило, возникают при износе подшипников, что вызывает радиальное биение ротора, который будет задевать обмотку статора и провоцировать возникновение короткого замыкания. О неисправности генератора можно судить по следующим признакам:
- Во время работы двигателя горит или мигает лампа разряда аккумуляторной батареи.
- Перезаряд аккумуляторной батареи или его регулярная разрядка.
- Тусклая работа фар и электроприборов во время работы двигателя.
- Сила света фар изменяется в зависимости от частоты оборотов двигателя.
- От генератора во время его работы слышатся посторонние звуки.
- Самая частая и простая неисправность — после пуска двигателя датчик показывает, что зарядки нет. Возможные причины:
- плохо натянут ремень привода генератора;
- обрыв в проводки, которая питает цепь возбуждения (использовать для этого вольтметр или контрольную лампочку);
- проверить исправность амперметра, остановить двигатель и включить все фары (исправный амперметр будет показывать разрядку).
Диагностирование генераторов осуществляют при помощи вольтметра, амперметра и нагрузочного устройства для задания эталонных нагрузочных режимов проверки, поскольку включение всех потребителей тока автомобиля при полностью заряженной батарее не обеспечивает полной загрузки генератора.
При проведении технического обслуживания запрещается:
- запускать двигатель, если отсоединен от генератора плюсовой провод, при этом может возникнуть опасное для выпрямителя напряжение;
- подсоединять АКБ неправильной полярности;
- допускать работу генератора при отсутствии АКБ;
- допускать отсоединения АКБ от сети при работающем двигателе и отключенных потребителях;
- проверять исправность генератора «искрой» путем внешнего замыкания между собой клемм регулятора напряжения или генератор питать от постороннего источника питания;
- соединять шину щеткодержателя, с «+» генератора или клеммами;
- проверять исправность генератора и всей электрической цепи автомобиля контрольной лампочкой или другими приборами, питаемыми напряжением более 36 Вольт при подключенном генераторе;
- допускать попадание воды или масла на генератор;
- допускать касания проводов корпуса регулятора напряжения.
При проведении ТО первое, на что следует обратить внимание — это натяжение ремня генератора. Если ремень слишком ослаблен, то будет иметь место так называемая «пробуксовка». При этом генератор не сможет нормально выполнять своих функций. Чтобы проверить натяжение, необходимо нажать пальцем в середине ремня с усилием 80-100 Н (8…10 кгс). Идеальный прогиб – не более 15 миллиметров (рисунок 2).
1 — ручка; 2 — шкала; 3 — бурт; 4 — втулка; 5 — планка
Рисунок 2 – Проверка натяжного ремня привода генератора и динамометр для проверки натяжения ремней привода
Далее – производится измерение напряжения на клеммах аккумулятора – на отключенном и заведенном двигателе. Измерение необходимо производить при средних оборотах двигателя. Напряжение на клеммах аккумуляторной батареи после запуска двигателя должно повыситься. Если это так, то генератор работоспособен и полностью исправен. И, следовательно, он дает необходимую энергию подзаряда. Нормальный уровень напряжения – 14,3…14,5 Вольта (зависит от модели транспортного средства).
Проверку и регулировку регулятора напряжения осуществляют при повышенной частоте вращения коленчатого вала двигателя и выключенной нагрузке (сила тока равна нулю или незначительна). При этом регулируемое напряжение, определяемое по показаниям вольтметра, должно также соответствовать нормативному, равному 13,8…14,1 В. При его несоответствии производят регулировку. Необходимо отметить, что повышение напряжения генератора выше расчетной на 10…12% снижает срок службы аккумуляторной батареи и осветительных приборов примерно в 2 раза.
Если реле-регулятор не поддается регулировке, его заменяют. Ограничивающее напряжение проверяют при включенных потребителях тока и повышенной частоте вращения коленчатого вала двигателя.
Проверка работоспособности диодного моста производится мультиметром в режиме измерения переменного напряжения. Мультиметр подключается к клеммам «В+» (или «30») на генераторе и к «массе» автомобиля (двигатель во время измерений должен быть заведен). Нормальный уровень напряжения должен составлять 0,5 Вольта. Если уровень напряжения выше, то можно делать вывод о неисправности диодного моста.
Если диодный мост целый, необходимо проверить целостность обмотки ротора генератора:
—с генератора снимается щеточный узел и измеряется сопротивление обмотки (мультиметр необходимо переключить на соответствующую шкалу). Для измерения щупы прикладываются к контактным кольцам. Нормальный уровень сопротивления – 5-10 Ом. При отсутствии цепи говорит об обрыве обмотки.
Далее следует замерить сопротивления между корпусом генератора и любым из контактных колец. В этом случае прибор должен показать максимальное сопротивление. Если же звучит «звонок» или сопротивление слишком малое, то обмотка, скорее всего, «сидит» на корпусе. Обмотки статора необходимо проверить аналогичным образом. Все замеры делаются при снятом диодном мосте.
Далее следует осмотреть щеточный узел генератора на факт залегания щеток и их износа. В случае, когда щетки выступают из щеткодержателя более, чем на 5 мм, необходимо заменить весь узел.
Изношенную щетку необходимо заменить новой и притереть ее по кольцу, для чего полоску стеклянной бумаги кладут гладкой стороной к кольцу, а к шероховатой стороне прижимают щетку. Двигая бумагу, притирают щетку соответственно кривизне кольца.
При проведении технического обслуживания со снятием генератора с двигателя автомобиля обязательно необходимо проверять высоту щеток. Она должна быть равна 8 миллиметров от основания щетки до пружины. При износе щеток более 0,5 миллиметров по диаметру, необходимо щетки заменить на новые. Также при этом необходимо обязательно проточить контактные кольца, минимальный диаметр которых должен составлять не менее 29,3 миллиметра.
3. Техническое обслуживание автомобильного стартера
Наиболее распространенные неисправности стартера:
1. Втягивающее реле (ВР) стартера не срабатывает, якорь не вращается. Причины:
- Потеря работоспособности, в том числе и полная (частичная) разрядка аккумуляторной батареи.
- Окисление контактных выводов АКБ, наконечников подключаемых к ним проводов.
- Недостаточный контакт наконечников с клеммами АКБ.
- Отсутствие контакта (переменный контакт) на клеммах ВР, вызванный обрывом проводов, соединяющих реле с выключателем зажигания и стартером.
- Межвитковое замыкание, обрыв или «пробой на массу» обмоток ВР.
- Заклинивание якоря втягивающего реле.
- Нарушение работоспособности контактора выключателя.
2. При пуске стартера и срабатывании ВР якорь вращается медленно или не вращается вообще.
- Потеря контакта на клеммных болтах ВР.
- Чрезмерный износ щеток или их «зависание».
- Воздействие высоких температур, или «подгорание» пластин коллектора.
- Нарушение целостности обмоток якоря (статора).
- Нарушение изоляции («пробой на массу») плюсового щеткодержателя.
- Замыкание между пластинами коллектора, вызванное нарушением изоляционного слоя.
- Межвитковое замыкание или «пробой на массу» обмоток якоря (статора).
Проверка работоспособности ВР выполняется следующим образом:
- В питающую цепь обмоток реле включают амперметр (вольтметр).
- Между шестерней привода и ограничительным кольцом вводят изолирующую прокладку, толщина которой составляет 13,0-15,0 миллиметров.
- На реле подают питающее напряжение.
- Снимают показания прибора, которые не должны превышать следующих значений: для силы тока – 23 Ампера, для напряжения – 9 Вольт. Превышение контрольных значений свидетельствует о повреждениях обмоток привода стартера или втягивающего реле.
Для проверки обмоток агрегата на предмет отсутствия «пробоев на массу» используют тестер, при его отсутствии – контрольную лампу. Выполняемые работы:
- Вывод обмотки возбуждения отключают от контакта ВР.
- Изолированные щетки фиксируют в приподнятом положении.
- Соединение неизолированного щеткодержателя и шунтовой катушки размыкают.
- Отворачивают винты, обеспечивающие фиксацию щеточных канатиков.
- Изолированные держатели освобождают от щеток.
- Контрольную лампу или тестер включают в цепь подачи напряжения величиной 12 Вольт.
Загорание лампы (отклонение стрелки тестера) свидетельствует о повреждениях изоляции обмотки возбуждения, вызывающих «пробой на массу». Этот метод используют и при проверке на наличие «пробоя» в изолированных щеткодержателях. В этом случае питающее напряжение подают на корпус стартера и изолированного щеткодержателя. При проверке коллектора (обмотки якоря) напряжение подают на корпус стартера и пластины коллектора. Во всех случаях отклонение стрелки (загорание сигнальной лампы) свидетельствуют о контакте обмоток с корпусом, или «пробое на массу».
3. Якорь включенного стартера вращается, однако коленвал силового агрегата неподвижен.
Причинами возникновения подобной ситуации могут стать:
- Проскальзывание (пробуксовка) муфты свободного хода (далее по тексту МСХ).
- Механическое повреждение элементов МСХ (буферной пружины, поводкового кольца).
- Выскакивание оси рычага включения или его механическое повреждение.
- Заклинивание (затрудненное перемещение) привода по винтовым нарезам вала якоря.
4. После пуска силовой установки стартер продолжает работать. В этом случае:
- выключить зажигание;
- в моторном отсеке отсоединить питающий кабель от ВР. Источником данной неисправности становятся:
- Заклинивание рычага привода.
- Механическое повреждение возвратной пружины включателя зажигания.
- Залипание контактов ВР или заклинивание привода стартера на валу якоря.
- Механическое повреждение, потеря эксплуатационных свойств (растяжка) возвратных пружин элементов стартера: втягивающего реле, МСХ.
- Заклинивание ВР.
- Перекос стартера, вызванный ослаблением креплений агрегата на корпусе силовой установки.
5. Повышенный уровень шума при вращении якоря. Основными источниками возникновения шума являются:
- Чрезмерно изношенные шейки и втулки вала якоря.
- Крышка стартера с повреждениями в районе привода.
- Зубья венца маховика силового агрегата или шестерня привода, имеющие механические повреждения.
- Ослабленные крепления стартера.
- Соприкосновение вращающегося якоря с полюсом, вызванное ослаблением крепления последнего в корпусе агрегата.
Признаки неисправности бендикса стартера:
- стартер жужжит, но не крутит двигатель;
- при запуске двигателя раздаётся скрежет стартера;
- стартер крутит, но не зацепляет маховик.
Кроме поломок бендикса, скрежет может говорить о выходе из строя деталей планетарного редуктора, а отсутствие зацепления с маховиком может быть вызвано поломкой вилки.
При техническом обслуживании следует проверить состояние зажимов, не допуская их загрязнения и ослабления крепления.
Стартер потребляет большой ток, поэтому даже незначительные переходные сопротивления в цепи стартера приводят к большому падению напряжения и снижению мощности стартера.
Следует особое внимание обратить на состояние коллектора и щеток. Щетки не должны заедать в щеткодержателях. Высота щеток должна быть не менее 5 мм. Усилие пружины должно быть в пределах 8,5…14 Н (0,85…1,4 кгс).
В случае загрязнения или незначительного обгорания коллектор следует зачищать мелкой стеклянной шкуркой зернистостью 80 или 100. При незначительной шероховатости коллектора и выступании изоляции между пластинами коллектор следует проточить на токарном станке.
После зачистки коллектора и контактов их продувают сжатым воздухом и проверяют плотность прилегания контактов. При значительной шероховатости коллектора стартера его следует отдать в ремонт. Щетки в щеткодержателях должны свободно перемещаться, не зависать и не иметь заметного качания. Не допускается применение щеток, пропитанных маслом или изношенных больше чем на 7 мм
Подгоревшие контакты электромагнитного реле стартера следует зачистить стеклянной шкуркой или плоским бархатным напильником, чтобы обеспечить соприкосновение по всей поверхности с контактным диском. Если контактные болты в местах соприкосновения с контактным диском имеют большой износ, их следует повернуть на 180°.
Величина тока, потребляемого стартером при его включении колеблется в пределах от 75А на холостом ходу до 800А при полном торможении якоря, а плотность тока под щетками при работе стартера составляет 60…100 а/см 2 .
Если якорь стартера после запуска двигателя остается в зацеплении с коленчатым валом, то скорость якоря может повыситься с 4500 об/мин · ? /30 рад/с до 10000 об/мин · ? /30 рад/с. и более. При этом обмотка якоря и ламели коллектора нагружаются большими центробежными силами, которые могут вызвать их разнос и обрыв. Даже весьма незначительный выход ламелей из коллектора (на величину до 0,01 мм ) сильно повышает износ щеток и коллектора. Опасность разноса якоря возрастает в связи с увеличением мощности стартера и диаметра его сердечника. Вследствие неравномерного износа щеток, ослабления или перекоса пружин и деформации щеткодержателей щетки зависают, и возникает искрение между ними и коллектором. При зависании одной из щеток плотность тока на другой увеличивается почти вдвое, при этом искрение и обгорание значительно возрастают, что может вызвать полный отказ в работе стартера. Искрение и обгорание щеток увеличиваются также при загрязнении щеток и коллектора, покрытии их продуктами износа (медно-графитной пылью) и при замасливании коллектора.
Расстояние между торцом шестерни и упором должно быть 3…5 мм (pиcунок 3). Этот зазор регулируется поворотом эксцентричной оси рычага привода. После регулировки нужно затянуть гайку оси, придерживая ось от поворота. Неисправность стартера, правильность его сборки и регулировки определяется:
- проверкой регулировки выключателя стартера;
- проверкой стартера на холостом ходу и при полном торможении
Рисунок 3 — Замер зазора от торца шестерни до чашки упорного кольца при полностью втянутом якоре тягового реле
Для проверки стартера необходимы хорошо заряженная аккумуляторная батарея, вольтметр постоянного тока со шкалой от 0 до 30 В, указатель постоянного тока с шунтом до 1000 А, тахометр со шкалой до 10 000 -1 и динамометр. Схема включения стартера показана на рисунке 24. Стартер соединяют с батареей (зажим стартера соединяют через указатель тока с плюсовым, а корпус стартера с минусовым выводом батареи). Для соединения стартера с батареей применяются провода сечением не менее 25—35 мм 2 . Силу тока и число оборотов якоря при испытании на холостом ходу измеряют не более чем через 30 с после включения стартера.
Стартер считается выдержавшим испытание, если при напряжении 12 В он потребляет ток не более 85 А и развивает частоту вращения не менее 400 мин -1 .
При тугом вращении якоря, которое обычно вызывается перекосами в результате неправильной сборки стартера, или задевания якоря за полюсы, или замыкания между витками, стартер потребляет ток большей силы, а обороты развивает меньше указанных. Малая сила потребляемого тока и пониженное число оборотов при нормальном напряжении на зажимах стартера свидетельствуют о плохом контакте в соединениях проводов или о недостаточном натяжении пружин щеток.
Для проверки стартера при полном торможении на шестерне привода закрепляют рычаг, соединенный с динамометром. Лучше использовать гидравлический динамометр. Тормозной момент М стартера определяется по формуле (1)
где L — длина рычага, м; Р — показание динамометра, кг.
Во избежание перегрева стартера испытание следует проводить в течение короткого времени. Если при заторможенной шестерне якорь вращается, то привод нужно сменить.
При проверке следует соблюдать осторожность, так как в момент включения стартера произойдет сильный рывок рычага, укрепленного на шестерне.
Исправный стартер при питании от полностью заряженной батареи потребляет ток не более 550 А при напряжении не менее 8 В и развивает момент 20,0 Н·м (2,0 кгс·м). Если потребляемый ток выше 550 А, а тормозной момент ниже 20,0 Н·м (2,0 кгс·м), это указывает на неисправность обмотки возбуждения. Если величина тормозного момента и сила потребляемого тока ниже нормальной, это при нормальном напряжении на зажимах стартера указывает на плохие электрические контакты стартера или слабое натяжение пружин щеток. Пониженное напряжение на зажимах стартера — менее 8,0 В — указывает на плохие контакты в проводах или на неисправность батареи.
1 — рычаг; 2 — динамометр; 3 — стартер; 4 — тяговое реле стартера; 5 — выключатель; 6 — указатель напряжения; 7 — указатель тока; 8 — шунт указателя тока; 9 — аккумуляторная батарея
Рисунок 4 — Схема включения при испытании стартера
ТО и текущий ремонт электрооборудования
11.1 ТО и ремонт системы зажигания и пуска двигателя
11.2 ТО и ремонт приборов освещения и сигнализации
11.3ТО и ремонт контрольно-измерительных приборов и дополнительного оборудования
На устранение неисправностей элементов электрооборудования автомобилей с бензиновыми и дизельными двигателями приходится от 11 до 17% от общего объема работ по ТО и ТР. Основное количество неисправностей приходится на аккумуляторную батарею, генератор с регулятором и стартер. Кроме того, особое внимание должно уделяться проверке и регулировке работы приборов освещения и сигнализации.
ТО и ремонт системы зажигания и пуска двигателя
Основные неисправности системы зажигания:
— система зажигания не обеспечивает достаточной мощности и бесперебойности искрообразования на свечах — при зтом наблюдается затрудненньїй запуск и неустойчивая работа даже прогретого двигателя, снижение его мощности и зкономичности, или ток високого напряжения вообще не поступает на свечи и происходит полньїй отказ в работе СЗ.
При диагностировании системи зажигания проверяют в основном следующие параметри:
— зазор между контактами прерывателя (при контактной системе
зажигания);
— начальний угол опережения зажигания;
— угол опережения зажигания, создаваемый центробежным или
вакуумным автоматом;
— угол поворота колснчатого вала двигателя, соответствующий замкнутому состоянию контактов прерывателя;
— форму осциллограмм напряжения первичной и вторичной цепей зажигания;
— пробивное напряжение на злектродах свечей зажигания.
Перед регулировкой зазора между контактами прерывателя проверяют состояние рабочей поверхности контактов. При существенном переносе металла с одного контакта на другой или при наличии нагара на контактах необходимо зачистить их плоским бархатным надфилем.
Для регулировки зазора между контактами прерывателя необходимо, вращая коленчатый вал, установить кулачок прерывателя в такое положение, при котором контакты будут максимально разомкнуты. Проверить щупом зазор А (рис. 11.1) и, если он превышает заданную величину, ослабить стопорные винты 3 и 4 крепления контактной панели, вставить отвертку в специальный паз и, поворачивая ее, установить нужный зазор, затем завернуть стопорные винты.
Рис. 11.1. Регулировка зазора между контактами распределителя:
1 — отвертка; 2 — распределитель; 3, 4 — винты; А — зазор между контактами
Одним из распространенных методов проверки момента зажигания является стробоскопический, при котором импульс высокого напряжения на свече первого цилиндра дает вспышку стробоскопической лампы в момент начала зажигания. При использовании стробоскопа необходимо один его зажим соединить с выводом Б катушки зажигания, подсоединить выводы питания и надеть на провод первого цилиндра датчик импульсов, затем установить на двигателе обороты холостого хода и направить мигающий поток света стробоскопа на метку шкива коленчатого вала.
Рис. 11.2. Установка момента зажигания:
1 — люк в картере сцепления; 2 — шкала (одно деление — 1 º ); 3 — метка на маховике
Практическую проверку правильности установки момента зажигания можно провести и непосредственно на автомобиле. Для этого необходимо запустить двигатель, прогреть его до нормальной температуры и, двигаясь со скоростью 50 км/ч на высшей передаче по ровной дороге, резко увеличить подачу топлива в двигатель резкого разгона. При этом в двигателе должны прослушиваться слабые непродолжительные металлические стуки; отсутствие стуков указывает на позднее зажигание, а не прекращающиеся стуки — на раннее зажигание.
Алгоритм действий принеисправности системы зажигания поедставлен на рисунке 11.3.
Рис. 11.3. Последовательность действий при поиске причины неисправности, если двигатель не пускается: I — направление поиска в топливной системе; II — направление поиска в системе зажиганий
В процессе эксплуатации в стартере возникают главным образом механические повреждения привода, связанные с пробуксовкой муфты свободного хода, износом или заклиниванием шестерни. Эти неисправности устраняются путем замены привода. Реже встречаются неисправности электрических цепей стартера, обусловленные окислением силовых контактов и контактов реле, обрывом обмоток, замасливанием коллектора, износом щеток. При этом ухудшается работа стартера, что вызывает необходимость его снятия и переборки.
У снятого стартера на специальном стенде проверяют развиваемый крутящий момент, потребляемый ток в рабочем режиме и в режиме полного торможения, частоту вращения якоря в рабочем режиме. Непосредственно на автомобиле у стартера также можно проверить потребляемый ток в режиме полного торможения, который увеличивается при замыкании цепей стартера на корпус и уменьшается при окислении контактов, щеток и коллектора. Однако указанный метод из-за его сложности на практике почти не применяется.
Техническое состояние электростартера оценивают по параметрам режимов холостого хода и полного торможения.
Испытание электростартера проводят на стендах. Схема для проверки стартера автомобиля ВАЗ дана на рис. 11.4.
Рис 11.4. Схема проверки стартера.
Текущий ремонт электрооборудования, системы зажигания и пуска автомобилей
При выполнении ТР автомобиля неисправные приборы электрооборудования снимают, очищают снаружи и диагностируют на специальных стендах, где проверяют их работоспособность и выявляют причину неисправности. Подлежащие ремонту агрегаты разбирают на узлы и детали, промывают в моющем растворе, заменяют или ремонтируют. После сборки агрегат проверяют на контрольном стенде. При этом выполняют следующие работы: устраняют замыкания, возникающие в результате повреждения изоляции катушек обмоток возбуждения и якоря, проверяют и перематывают обмотки, при задирах заменяют полюсные сердечники, протачивают коллектор.
Оборудование для ремонта электрооборудования:
— контрольно-испытательные стенды для проверки генераторов и стартеров;
— приборы системы зажигания;
— контрольно-измерительные приборы автомобилей;
— станки для проточки и фрезерования;
— ванны для мойки деталей;
— вспомогательными приспособлениями (прессы, точило и пр.).
ТО и ремонт приборов освещения и сигнализации
Неисправности приборов освещения и сигнализации связаны чаще всего с
перегоранием ламп или выходом из строя выключателей, переключателей, реле.
Наиболее сложными работами являются проверка и регулировка положения фар на автомобилях и их силы света, силы света других световых приборов, а также частоты включения указателей поворотов, что связано с безопасностью движения.
Положение фары на практике считается отрегулированным, если ее луч направлен вдоль оси дороги с захватом обочины и обеспечивает освещение на расстоянии порядка 30 м при ближнем свете и порядка 100 м — при дальнем. (ГОСТ 25478-91 регламентирует углы наклона луча фар при проверке в стационаре передвижным прибором.) Указатели поворотов должны работать в проблесковом режиме с частотой следования проблесков (1,5 ±0,5) Гц. Суммарная сила света фар (при дальнем свете), измеренная в направлении оси отсчета, должна быть не менее 10 000 кд. ГОСТ 25478-91 регламентирует также диапазоны силы света габаритных огней, сигналов торможения и указателей поворота.
Установку фар проверяют и регулируют на отдельном посту или на линии ТО при помощи настенного или переносного экрана или передвижных оптических приборов (см. рис. 11.5). Проверку частоты включения указателей поворотов проводят при помощи секундомера путем измерения времени не менее чем по десяти проблескам.
Рис. 11.5. Регулировка фар и направлення светового потока для автомобилей:
а — «КамАЗ» с колесной формулой 6×4; б — марки «КамАЗ» с колесной формулой 6 х 6; в — марки «ЗИЛ» с колесной формулой 4 х 2; І — линия высоты центров фар от уровня земли; II, IV — линии центра левой и правом фар; III — ось автомобиля
ТО и ремонт контрольно-измерительных приборов и дополнительного оборудования
Проверяют их общую работоспособность и правильность показаний. При выявлении неработающего прибора или его явно неправильных показаний проверяют на обрыв электрические цепи самого прибора, связанного с ним датчика и соединительных приводов. Вышедшие из строя приборы и датчики, как правило,заменяют.
Для диагностирования системы электрооборудования двигателя, а также других приборов электрооборудования автомобиля используются мотор-тестеры различного типа, приборы для диагностики отдельных агрегатов
Специальное оборудование для ТО и ремонта электрооборудования
Модель | Оборудование | Измеряемые диагностические параметры |
Э-240 | Контрольно-испытательный стснд для проверки генераторов, реле- регуляторов и стартеров | Напряжение, сила тока, омическое сопротивление, частота вращения, тормозной момент в режиме плавного торможения |
Э-102 | Стробоскопический прибор | Угол опережения зажигания |
Э-203 | Прибор для пескоструйной очистки и проверки свечей зажигания | Искрообразованис и герметичность свечи |
К-ЗОЗ, К-310, ПРАФ-3, НИИАТЭ-6, «ЕФЛЕ* | Прибор для проверки фар | Установка фар, сила света |
ИЭ-1 | Индикатор плотности | Плотность электролита |
Э-204 | Прибор для проверки контрольно-измерительных приборов | Показания контрольно-измерительных приборов автомобиля |
ЛЭ-2 | Нагрузочная вилка | ЭДС и напряжение под нагрузкой |
Э-107, Э-108 | Пробник | — |
Рис. 11.6. Схема подключения мотор-тсстера к системам автомобиля:
1 – мотор-тестер; 2 — стробоскопическая лампа; 3 — свсчи зажигания;
4 — распределитель зажигания; 5 — катушка зажигания; 6 — аккумуляторная батарея;
7 — зонд измерения СО
1. Каковы основные неисправности аккумуляторных батарей и их причины?
2. Как диагностируют техническое состояние аккумуляторных батарей?
3. Как приготовить электролит?
4. Как заряжают аккумуляторные батареи?
5. Какие работы выполняются при ТО генераторных установок и реле-
регуляторов?
6. Какие работы выполняются при ТО приборов зажигания?
7. Какие работы выполняются при ТО стартеров?
8. Какие работы выполняются при ТО приборов освещения, сигнализации и
контрольно-измерительных?
9. Каковы особенности ТО обслуживания контактно-транзисторных систем
зажигания?
10. Как установить зажигание?
Организация и управление производством технического обслуживания и текущего ремонта автомобилей.
Общая характеристика современных АТП (Государственного и частного подчинения).
Общая характеристика технологического процесса ТО и ремонта автомобилей в АТП.
Общая характеристика современных АТП
В зависимости от производственных функций предприятия автомобильного транспорта подразделяются наавтотранспортные, автообслуживающие и авторемонтные.
Автотранспортное предприятие (АТП) осуществляет перевозку грузов и пассажиров, а также все производственные функции по ТО, ремонту, хранению и снабжению подвижного состава.
По своему назначению АТП делятся на грузовые, пассажирские (автобусные и легковые), смешанные и специальные (скорой медицинской помощи, коммунального обслуживания и др.).
По организации производственной деятельности АТП, кроме автотранспортных служб колхозов, подразделяются на: комплексные, которые осуществляют транспортную работу, все виды ТО и TP и хранение подвижного состава, кооперированные, деятельность которых осуществляется с учетом централизации производства транспортной работы, а также централизации (полной или частичной) работ по ТО и ТР.
Наиболее распространены комплексные АТП с количеством автомобилей 200-400 единиц. К кооперированным АТП относятся автокомбинаты. Они насчитывают 700-1000 и более единиц подвижного состава и состоят из основного предприятия и нескольких филиалов (на 150-200 и более единиц), расположенных на других территориях – в районе обслуживания перевозками.
На основном предприятии выполняются наиболее трудоемкие и сложные виды технического обслуживания (ТО-2), диагностики и TP всего подвижного состава, а также все виды ТО, ремонт и хранение гой части подвижного состава, которая базируется на основном предприятии. В филиалах производятся хранение подвижного состава, техническое обслуживание в объеме EO и TO-1 и несложный ТР. Автокомбинаты способствуют приближению подвижного состава к потребителям, сокращению нулевых пробегов, а также ликвидации малоэффективных мелких предприятий.
Автообслуживающее предприятие является специализированнымАТП, выполняющим лишь производственные функции по ТО и ремонту подвижного состава.
К автообслуживающим предприятиям относятся базы централизованного обслуживания, станции технического обслуживания (СТО), гаражи-стоянки (гостиницы для автотуристовмотели, лагеря для автотуристов — кемпинги), а также автозаправочные станции.
Базы централизованного технического обслуживания
(БЦТО) предназначены для централизованного выполнения сложных видов ТО и крупного текущего ремонта подвижного состава, эксплуатируемого небольшими по размеру АТП.
В объем ремонтных работ, выполняемых базами, входит замена агрегатов, требующих капитального ремонта, на агрегаты, отремонтированные на авторемонтном предприятии и находящиеся в централизованном оборотном фонде базы. Кроме того, на базах может быть организован централизованный ремонт отдельных механизмов, узлов, агрегатов и приборов автомобилей.
Станции технического обслуживания (СТО) имеют своим назначением обслуживание автомобилей индивидуальных владельцев, выполнение как отдельных работ, так и всего объема (по видам) ТО, ремонт автомобилей и снабжение их запасными частями, принадлежностями и эксплуатационными материалами.
Гаражи-стоянки (Г-С) являются предприятиями для хранения автомобилей. Иногда они выполняют техническое обслуживание автомобилей и снабжение их эксплуатационными материалами.
Гаражи-стоянки общего пользования предназначены преимущественно для хранения автомобилей индивидуальных владельцев. Такие стоянки могут быть домовыми, квартальными и районными, устраиваемыми в виде специальных зданий или открытых площадок. Стоянки этого типа строят также для временного хранения автомобилей в местах большого их скопления и для разгрузки улиц и площадей города (например, у стадионов, вокзалов). К этому типу предприятий относятс автогостиницы (мотели) и кемпинги – гаражи-стоянки для временного хранения автомобилей туристов.
Автозаправочные станции (АЗС) являются предприятиями по снабжению автомобилей эксплуатационными материалами, преимущественно топливом, а также маслами, консистентными смазками, водой, антифризом и иногда воздухом для шин.
Обычно станции специализируются по роду автомобильного топлива: бензиновые, дизельные, газобаллонные.
Станции АЗС подразделяются на городские и придорожные. Величина заправочных станций измеряется максимальным суточным количеством заправок, соответствующим для городских станций от 500 до 2000 и для придорожных от 500 до 1000 заправок.
Авторемонтные предприятия являются также специализированными предприятиями, производящими ремонт (восстановление) автомобилей и агрегатов.
К ним относятся авторемонтные и агрегатно-ремонтные заводы и базы централизованного ремонта узлов агрегатов, авторемонтные мастерские, шиноремонтные мастерские или заводы, аккумуляторные зарядно-ремонтные станции и специализированные цехи.
Специализированные мастерские и цехи выполняют ремонт узлов и механизмов автомобиля, а также окрасочные, кузовные и другие работы, обслуживая эксплуатационные предприятия в централизованном порядке.
Структура комплексного АТП
Как уже было отмечено выше, комплексные автотранспортные предприятия (автобазы, автоколонны, легковые и автобусные парки) наряду с транспортной деятельностью осуществляют полностью или частично работы по заправке, хранению, материально-техническому снабжению, техническому обслуживанию и ремонту подвижного состава. Для этого они имеют гаражи-стоянки, бензо- и маслозаправочные станции, материально-технические склады, профилактории и мастерские для технического обслуживания и ремонта подвижного состава.
Рис. 13.1. Структура комплексного автотранспортного предприятия.
Прибытие автомобилей с линии происходит, как правило, в течение относительно короткого времени. Так как пропускная способность EO рассчитывается на одну или две рабочие смены, то большая часть автомобилей после приема направляется в зону хранения, откуда в порядке очереди они поступают в зону EO и далее в соответствии с графиком (рис. 13.2).
По прибытии автомобилей в ATO водители сообщают механикам, принимающим автомобили с линии, о замеченных неисправностях. Механики ATO или автоколонны субъективно и при помоги средств диагностирования определяют техническое состояние автомобилей. По результатам диагностирования в ATO оформляют соответствующую документацию («Ремонтный листок»).
Рис. 13.2. Схема производственного процесса АТП.
При необходимости дальнейшего уточнения диагноза автомобили после проведения уборочно-моечных работ (УМР) направляют на посты диагностики Д-1 или Д-2. Для этой цели могут быть использованы эксперты (высококвалифицированные ремонтные рабочие). Исправные автомобили, не подлежащие плановому обслуживанию, направляют в зону хранения, а подлежащие TO-1 или ТО-2 — соответственно на Д-1 или Д-2.
Функции основных производственных подразделений по ТО и ремонту представлены в табл. 13.1.
Функции производственных подразделений по ТО и ТР автомобилей
Подразделение | Производственные, информационные функции, принимаемые решения |
Контрольно- технический пункт (КТП) | Выявление из общего потока неисправных автомобилей и определение у них отклонений параметров технического состояния механизмов, обеспечивающих безопасность движения |
Комплекс EO | Проведение работ EO |
Продолжение табл. 13.1.
Подразделение | Производственные, информационные функции, принимаемые решения |
Комплекс углубленной диагностики (Д-2) | Проведение регулировочных работ и определение неисправностей в соответствии с перечнем работ комплекса Д-2. Уточнение причин отказов и отклонений от нормативных диагностических параметров технического состояния узлов, агрегатов и систем, эксплуатационных свойств автомобиля |
Комплекс общей диагностики с TO-1 (Д-1 с ТО-1) | Хранение автомобилей в ожидании ТО-1. Проведение работ по ТО-1. Определение при TO-1 отклонений от нормативных значений диагностических параметров |
Комплекс ТО-2 с диагностикой Дто-2 (ТО-2 с Дто-2) | Хранение автомобилей в ожидании ТО-2. Проведение работ по ТО-2. Уточнение при ТО-2 причин отказов и отклонений от нормативных диагностических параметров технического состояния автомобилей |
Комплекс диагностики перед TP (Дтр) | Уточнение при TP отклонений диагностических параметров технического состояния автомобилей. Уточнение выявленных на ТП причин отказов и отклонений от нормативных диагностических параметров технического состояния автомобилей |
Комплекс TP с диагностикой TP, Дтр | Хранение автомобилей в ожидании ТР. Проведение работ по TP автомобилей. Определение при TP отклонений от нормативных диагностических параметров технического состояния автомобилей |
Комплекс технического контроля (Дот) | Уточнение после TP, ТО-1, ТО-2 значений отклонений от нормативных диагностических параметров технического состояния и эксплуатационныхсвойств автомобилей |
Общая характеристика технологического процесса ТО и ремонта автомобилей в АТП.
Техническое обслуживание представляет собой совокупность работ определенного назначения, каждая из которых, в свою очередь, состоит из операций, выполняемых в определенной технологической последовательности, составляющей в целом технологический процесс.
Операция — это комплекс последовательных действий по обслуживанию агрегата или группы агрегатов автомобиля (например, смена масла в картере двигателя, регулировка сцепления и др.). Таким образом, подтехнологическим процессом ТО автомобиля понимается определенная последовательность выполнения работ и операций, имеющих своей целью поддержание работоспособности автомобиля.
Основной задачей технологического процесса ТО является высокое качество выполняемых работ при наименьшей затрате рабочего времени, а следовательно, при наибольшей производительности труда рабочего.
Независимо от вида ТО, за исключением EO, оно содержит следующие основные работы: уборочно-моечные и обтирочные (внешний уход), контрольно-диагностические, контрольно-крепежные, регулировочные, электротехнические, смазочно-очистительные, шинные и заправочные. Кроме того, в комплекс работ по ТО входят: контрольно-осмотровые работы
перед EO, TO-1 и ТО-2 и работы по проверке автомобиля после выполнения обслуживания.
Уборочно-моечные и обтирочные работы заключаются во внутренней уборке кабины водителя, платформы грузового автомобиля или внутреннего салона кузова легкового автомобиля и автобуса; наружной мойке шасси и кузова автомобиля и протирке его наружных частей, боковых и передних стекол.
Контрольно-диагностические работы заключаются в контроле состояния или работоспособности агрегатов, механизмов, приборов, систем и автомобиля в целом по внешним признакам (выходным параметрам) без разборки или вскрытия механизмов (рис. 13.3.).
Рис. 13.3. Схема контрольно-диагностическихработ при ТО автомобиля.
Регулировочные работы включают регулировочные операции по восстановлению работоспособности агрегатов, механизмов и систем автомобиля с помощью предусмотренных в них регулировочных устройств, до уровня, требуемого правилами технической эксплуатации автомобиля или техническими условиями (например, частоты оборотов коленчатого вала двигателя на холостом ходу, свободного хода педали сцепления и др.).
Крепежные работы состоят из проверки состояния резьбовых соединений деталей (болтов, шпилек, шплинтов) и крепления их (подтяжки), постановки крепежных деталей взамен утерянных и замены негодных.
Электротехнические работы заключаются в проверке внешнего состояния источников электроэнергии (аккумуляторной батареи, генератора с реле-регулятором и выпрямителем переменного тока) и потребителей электроэнергии (приборов батарейной системы зажигания, стартера, приборов освещения и сигнализации и контрольных измерительных приборов), очистки от пыли, грязи и следов окисления контактных соединений, устранения неисправностей в результате диагностирования систем электрооборудования автомобиля.
Работы по системе питания двигателя включают проверку внешнего состояния приборов системы питания (карбюратора, топливного насоса, воздушного фильтра и др.), герметичности трубопроводов, устранение неисправностей и регулировку по результатам диагностики.
Смазочно-очистительные работы включают периодическое пополнение и смену масла в картерах агрегатов (двигателе, коробке перемены передач и др.), смазку подшипников и шарнирных соединений трансмиссии, ходовой части, рулевого управления и кузова, заправку автомобиля специальными жидкостями (тормозной, амортизаторной), очистку всех фильтров, замену фильтрующих элементов и отстойников системы смазки.
Шинные работы состоят из проверки внешнего состояния шин (покрышек) с целью установления необходимости ремонта, удаления из протектора покрышек застрявших острых предметов, проверки внутреннего давления и доведения его до необходимого. Кроме того, шинные работы при ТО могут включать перестановку и замену шин.
Контрольные работы после обслуживания состоят из проверки работы двигателя, действия тормозов управления и других агрегатов и механизмов.
Заправочные работы включают заправку топливного бака автомобиля и пополнение жидкостью системы охлаждения двигателя.
Такое подразделение основных работ ТО обусловливает, вопервых, использование рабочих соответствующей специальности и квалификации при выполнении каждого вида работ и, вовторых, применение специального оборудования приборов и инструмента на месте выполнения указанных работ. Кроме того, это необходимо для организации рационального, последовательного их выполнения.
Независимо от вида ТО первоочередными являются уборочно-моечные работы, одной из задач которых является подготовка автомобиля к последующим операциям ТО и придание ему надлежащего внешнего вида.
Заправка автомобиля топливом может производиться перед выездом на линию или перед постановкой его на стоянку.
Территория помещения, предназначенная для выполнения одной или нескольких однородных работ или операций процесса ТО или ремонта, оснащенная приборами, приспособлениями, инструментами и другим оборудованием, называетсярабочим постом.
Производственный участок на рабочем посту, обслуживаемый одним рабочим, называетсярабочим местом. Рабочий пост может состоять из одного или нескольких рабочих мест.
Производственно-техническая база АТП
Перед въездом на территорию АТП автомобиль проходит через контрольно-пропускной пункт (КПП), где его осматривает дежурный механик. Затем в зоне ЕО автомобиль убирают, моют и обтирают, т. е. готовят к эксплуатации на следующий день. Эти работы выполняют обычно на нескольких последовательно расположенных площадках- постах.
Отдельное помещение выделяется на АТП для проведения ТО-1. Одновременно в зоне обслуживают несколько автомобилей, располагают их обычно один за другим. Большую площадь занимают зоны ТО-2 и текущего ремонта, которые часто объединены в одном помещении. В этих зонах автомобили стоят сравнительно долго, и поэтому их располагают так, чтобы автомобили не мешали друг другу при въезде и выезде, а рабочим было удобно работать.
Техническое состояние автомобилей проверяют, как правило, перед направлением их в зоны ТО-1, ТО-2 или текущего ремонта. Эти работы проводят в пункте диагностики. Повторному контролю автомобиль может быть подвергнут и после обслуживания и ремонта, а поэтому пункт диагностики находится или вблизи технических зон, или в отдельном здании недалеко от производственного корпуса АТП.
В подсобных производственных отделениях (цехах) АТП производят контроль и ремонт деталей и узлов, снятых с автомобилей. Одни отделения обслуживают только ремонтную зону предприятия, а другие, кроме ремонтных работ, осуществляют профилактические работы. К последним отделениям относят электротехническое, аккумуляторное, шиномонтажное и отделение по уходу за системой питания.
Электротехническое отделение предназначено для технического обслуживания и мелкого текущего ремонта приборов электрооборудования автомобиля (свечей зажигания, прерывателей-распределителей, генераторов, стартеров, фар и т. п.). Основным оборудованием являются стенды и приборы для проверки электрооборудования. Электрики выполняют частичную разборку и сборку, замену неисправных деталей, проверку на стендах, регулировку и другие работы по приборам электрооборудования.
В аккумуляторном отделении выполняют профилактические работы по уходу за аккумуляторными батареями. По характеру труда этот цех является вредным. На крупных предприятиях отделение может состоять из четырех технологически связанных между собой помещений. В основном помещении выполняют контроль и мелкий ремонт аккумуляторов. Отсюда большая часть аккумуляторов поступает в зарядное помещение для подзарядки, где находятся выпрямители и стеллажи для батарей с вытяжными устройствами. Отдельное помещение занимает кислотная. Здесь вырабатывается дистиллированная вода, разбавляется кислота и приготовляется электролит. В четвертом помещении — кладовой — могут храниться готовые и требующие подзаряда аккумуляторные батареи, бутыли и некоторые детали.
Отделение по уходу за системой питания называют карбюраторным отделением или отделением топливной аппаратуры (для дизельных автомобилей). На специальных стендах проверяют работу карбюраторов, насосов, форсунок, топливных и воздушных фильтров. Кроме контрольных операций, здесь производят очистку, регулировку приборов системы питания и замену мелких деталей.
Рабочие шиномонтажного отделения производят монтаж и демонтаж шин, контролируют их состояние, осуществляют балансировку колес, ремонтируют и подкрашивают диски колес, ремонтируют камеры, следят за перестановкой шин, сдают в ремонт и получают отремонтированные шины. Все эти работы являются трудоемкими, а поэтому в отделении устанавливают различные приборы и стенды: для монтажа и демонтажа шин, компрессоры, борторасширители, вулканизаторы, стенд для балансировки, тельфер и др.
Другая большая часть отделений (цехов) предназначена только для текущего ремонта автомобиля. К ним относятся: агрегатное, слесарно-механическое, тепловое, арматурно-кузовное, обойное, малярное и другие отделения. Наиболее трудоемкие и ответственные работы по текущему ремонту автомобилей выполняются в агрегатном и слесарно-механическом отделениях АТП.
В агрегатное отделение поступают снятые с автомобиля неисправные агрегаты, где они частично разбираются на стендах. Снятые детали ремонтируются в других цехах, заменяются новыми или ранее восстановленными (из оборотного фонда). При разборке и сборке применяют монтажно-демонтажный инструмент, а после мойки и обезжиривания деталей для определения величины износа используют контрольно-измерительный инструмент и приборы. От качества работы слесарей этого отделения зависит надежность и долговечность агрегатов автомобиля.
Большинство деталей, требующих восстановления, передается из агрегатного отделения в слесарно-механическое. Сюда же поступают детали для механической обработки из сварочного и других цехов. Отделение состоит из слесарного и механического участков. Слесарный участок предназначен для холодной обработки деталей ручным инструментом. В качестве последнего используют зубила, напильники, молотки, ножовки, дрели, зенковки, развертки, метчики, плашки, шаберы и другой инструмент.
Большинство работ слесари выполняют у верстаков с тисками и столов с правочными и разметочными плитами. В механическом участке обрабатывают детали при помощи токарных, фрезерных, шлифовальных, строгальных, сверлильных и других станков.
Тепловой участок автотранспортного предприятия включает в себя отделения: кузнечно-рессорное, сварочное, медницкое и жестяницкое. Работы здесь выполняют с применением открытого огня, а поэтому их считают опасными в пожарном отношении. На крупных предприятиях каждое отделение занимает самостоятельное помещение.
Кузнечно-рессорное отделение предназначено для восстановления металлических деталей путем их механической обработки на наковальне, плите или под прессом пневматического молота после нагрева металла в горне или термической печи. Кроме того, в этом отделении закаливают, подвергают цементации и другим видам термической обработки восстанавливаемые детали. В этом цехе ремонтируют рессоры, пружины, рулевые тяги, балки, шатуны, цапфы, рычаги, поворотные стойки и т. п.
В сварочном отделении режут металл, сваривают поломанные детали, заваривают трещины, наплавляют слой металла на изношенную поверхность. Для восстановления деталей из тонколистового металла и серого чугуна, а также для наплавки применяют газовую (ацетилено-кислородную) сварку. Электродуговая сварка используется для заварки трещин (рама, балки), соединения двух деталей из стали и чугуна сложной конфигурации и для ремонта деталей из алюминиевых сплавов. Ацетиленовый генератор для газовых работ размещается в отдельном помещении. Рабочие места сварщиков изолируют от остальной части теплового участка несгораемой занавесью или металлическим экраном. Сварочные работы являются вредными.
В медницком цехе ремонтируют детали автомобиля, изготовленные из цветных металлов и сплавов (радиаторы, топливо- и маслопроводы, вкладыши подшипников и т. п.). Основным рабочим инструментом медников является паяльник. Здесь же радиаторы очищают, проверяют герметичность и целость трубок и полостей. Часть работ, например, пайку и расплавку выполняют на столах с вентиляционным вытяжным устройством.
Рабочие жестяницкого отделения выполняют текущий ремонт деталей, изготовленных из листовой стали (части кузова, кабины, оперения, капота, брызговиков, кожухов и др.). Инструмент жестянщика состоит из набора специальных оправок, болванок, растяжек и молотков, при помощи которых выравнивают листовой металл и восстанавливают первоначальные формы деталей. В цехе можно производить газовую и точечную сварку металла.
Ряд отделений специализируется на восстановлении деталей кузова автомобиля. Работы кузовного отделения имеют много общего с работами жестяницкого цеха, а поэтому в грузовых АТП эти отделения объединяют в одном месте. В крупных пассажирских предприятиях кузовное отделение существует самостоятельно, куда может вводиться автомобиль для выполнения текущего ремонта.
Если предприятие небольшое, то здесь же в кузовном отделении выполняют и арматурные работы. В этом отделении ремонтируют арматуру автомобиля: декоративные накладки, петли, замки, стеклоподъемники, стеклоочистители, вставляют стекла. Работы выполняются в основном у автомобиля и сводятся к регулировке и замене отдельных неисправных деталей.
Столярное отделение организуют на АТП для ремонта деревянных платформ грузовых автомобилей. При большом объеме работ платформа кузова может размещаться в помещении отделения, для чего используют транспортные тележки, стенды, тельферы.
В обойном отделении рабочие восстанавливают подушки сидений и спинок, заменяют внутреннюю обивку салона кузова, а также могут изготавливать утеплительные чехлы. Основные работы в цехе выполняют на верстаках, а из механического оборудования используют швейную машину и стенд-пресс для сборки подушек.
Малярное отделение состоит из трех самостоятельных в технологическом отношении участков: подготовительного, окрасочного и сушильного, На первом участке отдельные детали и кузов готовят к окраске, где удаляют старую краску, обезжиривают, грунтуют шпатлюют и шлифуют поверхность. Затем автомобиль окрашивают (иногда в специальных камерах) и подвергают сушке или при помощи передвижных терморадиационных установок, или в специальных сушильных камерах. Малярный цех оборудуют мощной приточно-вытяжной вентиляцией с очисткой отсасываемого воздуха в гидрофильтрах.
На крупных АТП имеются шиноремонтные (вулканизационные) отделения, в которых путем горячей вулканизации восстанавливают камеры и покрышки. Для этого цех оборудуют парогенератором, секторными мульдами, шероховальным станком, борторасширителем, подъемными устройствами и т. п.
Для снабжения всех отделений и зон автотранспортного предприятия материалами и запасными частями на его территории создают складские помещения. К ним относятся склады запасных частей, агрегатов, шин, смазочных материалов, жидкого топлива, угля, инструментов (инструментальная кладовая) и промежуточный.
Для обеспечения нормальной деятельности всех производственных отделений АТП в качестве самостоятельного подразделения действует отдел главного механика (ОГМ). Работники этого отдела следят за техническим состоянием зданий, сооружений, оборудования, коммуникаций и при необходимости выполняют их ремонт и профилактические осмотры.
На крупных предприятиях при ОГМ могут создаваться следующие самостоятельные группы: механическая – ремонт технологического оборудования и изготовление несложных нестандартных приспособлений; строительная – ремонт зданий и сооружений (столярные, кровельные, стекольные, каменные, земляные, малярные и другие работы); электротехническая – ремонт силового и осветительного электрооборудования; сантехническая – ремонт и эксплуатация отопления, водопровода, канализации; внедрения новой техники – монтаж, установка и пуск нового оборудования.
Рекомендованная к изучению литература:
Основная
1. Бернадский В.В. Техническое обслуживание и ремонт автомобилей.
– Ростов н/Д: Феникс, 2007. – 456с.
2. Лудченко О. А. Технічне обслуговування і ремонт автомобілів:
Організація і управління:Підручник.
– К.: Знання – Прес, 2004.- 478с.
3. Несвитский Я. И. Техническая эксплуатация автомобилей.
– К.: „Вища школа”, 1971, 428 с.
4.Техническое обслуживание и ремонт автомобилей:Учебник для студ. сред.проф. образования / В.М.Власов,С.В.Жанказиев,С.М.Круглов
и др.; Под ред. В.М.Власова.
– М.: Издательский центр«Академия», 2004. – 480с.
5. Техническая эксплуатация автомобилей: Учебник для вузов /
Е.С.Кузнецов, В.П.Воронов, А.П.Болдин и др.; Под ред. Е.С.Кузнецова.
– М.:Транспорт, 1991. – 413с.
6. Туревский И.С. Техническое обслуживание автомобилей.Книга 2.
Организация хранения, технического обслуживания и ремонта автомобильного транспорта:Учебное пособие.
– М.: ФОРУМ:ИНФРА-М, 2005. – 256с.
7. Туревский И.С. Техническое обслуживание автомобилей зарубежного
производства: учебное пособие.
– М.:ИД «ФОРУМ»: ИНФРА–М, 2007.–208с.
8. Чижков Ю. П., Акимов С. В. Электооборудование автомобилей. Учебник для ВУЗов. – М.:Издательство «За рулем»,1999. – 384 с.
9. Газарян А.А. Техническое обслуживание автомобилей.
10. Костів Б. І. Експлуатація автомобільного транспорту: Підручник.
– Львів: Світ, 2004. – 496с.; іл.
11. Лудченко А.А.,Сова И.П.Техническое обслуживание и ремонт автомобилей. – Киев: В шк, 1977. – 285 с.
12. Техническое обслуживание и ремонт автомобилей. / А.А. Лудченко,
И.П. Сова. – Киев: Вища школа, 1977. – 312 с.
13. Техническая эксплуатация автомобилей: Учебник для вузов/ Под ред. Г.В. Крамаренко. – М.: Транспорт, 1983. – 488 с.
Как отремонтировать электропроводку автомобиля?
Неисправности проводки автомобиля приводят к серьезным проблемам при эксплуатации машины – от некорректной работы датчиков и устройств, бортового компьютера и автоматики до полного выхода из строя дорогостоящего электрооборудования. Помните, что короткое замыкание цепей бортовой сети может привести к возгоранию автомобиля. Поэтому неисправности электрооборудования и электрики следует устранять сразу же при их обнаружении – не стоит откладывать ремонтные работы «в долгий ящик».
Выполнить ремонт электропроводки автомобилей можно как самостоятельно, так и в автосервисе. Основная трудность заключается в поиске неисправностей – обрывов, вышедших из строя реле, предохранителей и блоков, поломок отдельных элементов и устройств автоэлектрики.
Распространенные неисправности электрооборудования машины
К автоэлектрике относятся различные системы, детали, устройства и элементы транспортного средства – система зажигания, аккумулятор и генератор, цепи бортового компьютера, предохранители, датчики, блоки реле, различные электронные датчики, автосвет, а также автоэлектроника – климатическая система, аудиосистема, автоматика и системы безопасности. Необходимо учитывать особенности автомобильной электропроводки для того, чтобы оперативно найти и устранить неисправность в бортовой сети.
К часто встречающимся проблемам с электрооборудованием относятся:
- Выход из строя аккумулятора. Это может быть следствием недостаточной плотности электролита, повреждений корпуса с протечкой электролита, разрушения пластин, значительного окисления клемм аккумулятора.
- Поломки генератора — обрывы обмоток, проблемы с реле напряжения, выход из строя диодного моста, износ щеток, подшипника.
- Проблемы с системой зажигания. Речь идёт о неисправностях свечей, катушки зажигания, об обрыве цепи или окислении контактной группы.
- Деформации электропроводки — окисление в местах соединения (вводах, контактах, клеммах), обрывы, разрушение изоляции проводов, короткое замыкание проводки, нарушение целостности скруток.
- Выход из строя компонентов электроники. Имеются в виду неисправности различных электротехнических приборов в цепях, устройствах и электрооборудовании авто (проводники, диоды, предохранители, конденсаторы).
Как проверить проводку
Провести диагностику электрооборудования можно с помощью вольтметра, омметра или мультиметра, специальных диагностических стендов. Проводится и компьютерная диагностика, во время которой происходит считывание кодов ошибок и основных показателей бортовой сети машины. Для самостоятельной проверки цепей и поиска неисправностей электрики достаточно одного мультиметра или сигнальной лампы.
Используем мультиметр
Предохранители в бортовой сети считаются наиболее «слабым» звеном в плане долговечности. При нештатных ситуациях (например, при коротком замыкании) предохранительные элементы «берут удар на себя», защищая остальную электрику и электрооборудование машины. Предохранители восстановлению не подлежат и во время ремонта заменяются.
Проверяем напряжение
Перед тем, как проверить проводку в автомобиле, необходимо замерить напряжение электрической цепи между отдельными компонентами и электрооборудованием. Прозвонить можно так:
- Установить мультиметр в режим вольтметра.
- Подсоединить один щуп измерительного прибора к «минусу» аккумуляторной батарее либо к массе машины.
- Второй щуп подсоединить к подающему проводу цепи.
Если на дисплее прибора появляется определенное значение, то на данном участке цепи электрической схемы есть напряжение. Можно сравнить значения с требуемыми в соответствии с руководством по эксплуатации автомобиля.
Ищем короткое замыкание
После измерения напряжения выполняют поиск короткого замыкания цепей. Для этого потребуются либо мультиметр, либо сигнальная лампа. Что касается лампы, то при исправной проводке и отсутствии замыкания она не должна загораться.
Замыкание проводки, как и отсутствие напряжения (нулевое или бесконечное сопротивление в электрической цепи), свидетельствует о неисправностях в одном из 2-х компонентов:
- Потребителя – электрооборудования, устройств, предохранителей, блоков.
- Проводки – обрыв или замыкание проводов, плохие контакты проводки в месте соединения с потребителем.
Проверку на замыкание можно выполнить и в режиме вольтметра. Для этого на проверяемом участке необходимо извлечь все предохранители, подключить щуп к клеммам предохранительного элемента. Значение «0» на экране свидетельствует о наличии замыкания в цепи. Если при попытке пошевелить провода в цепи появляется напряжение, значит, замыкание вызвано именно проводкой, потребуется замена проводов.
Проверяем качество заземления
В автомобилях используется однопроводная схема электропроводки – это означает, что «минус» идет на массу (кузов) машины. Однако коррозия металлических деталей, их окисление и разрушение, «разбалтывание» приводят к нарушению заземления и, как следствие, к нарушению контактов бортовой цепи.
Проверка заземления, как и других элементов электрики авто, осуществляется с помощью мультиметра. Порядок действий следующий:
- Отключение АКБ.
- Подсоединение одного щупа мультиметра к кузову (металлическим деталям) машины.
- Подсоединение второго щупа к заземляющему элементу или месту соединения проводки.
Выведенное на экран прибора значение следует сравнить с заводскими данными (руководство по эксплуатации авто). Если значения сильно расходятся, то необходимо провести восстановление заземления – зачистить металл в месте соединения, проверить надежность крепления.
Проверяем целостность цепи
Соединение проводов в электрической цепи автомобилей – одно самых уязвимых мест во всей электрике машины. Помимо разрушения изоляции, нарушения целостности и обрывов в местах соединения здесь также нередко возникает окисление контактов. Определить дефекты можно не только с помощью измерительного прибора, но и визуально. Если целостность цепи нарушена именно в месте соединения, то потребуется пайка проводов с разъемами. В противном случае необходимо найти поврежденный участок, для чего понадобятся сигнальная лампа или мультиметр.
Ремонт электропроводки автомобиля
Прозвонку и восстановление электропроводки автомобиля можно выполнить самостоятельно или в автосервисе. После определения неисправных участков, где имеются повреждение проводов, замыкание или обрыв, осуществляют их пайку либо полную замену. Обычная скрутка с последующим обжимом является не полноценным ремонтом, а лишь временной мерой – учитывайте это, если у вас нет возможности припаять места обрывов.
Провода подбираются с такими же характеристиками, что и имеющиеся поврежденные (сопротивление, металл). Не следует устанавливать слишком длинные провода с «запасом», перекрученная открытая проводка под действием негативных факторов (перепады температур, влага, грязь) быстрее разрушается — это может привести к короткому замыканию цепи. При замене жгутов проводов с разъемами убедитесь, что контактные группы перед работами полностью зачищены от окисления.
Уязвимым элементом электрики авто также считаются монтажные блоки, расположенные в подкапотном пространстве. Из-за разрушающего воздействия перепадов температур и влаги возможно нарушение защитного покрытия и последующих дефектов дорожек, разъемов для подключения жгутов проводов, реле, конденсаторов. Ремонт монтажных блоков, состоящих из монтажных плат, предохранителей и электротехнических компонентов, включает в себя пайку для восстановления дорожек и покрытие специальным защитным лаком, а также замену неисправных элементов и проводки, разъемов, зачистку контактных групп от загрязнений, окислений.
Замена проводки авто
При замене проводки в автомобиле обязательно отключают питание, в том числе отсоединяют и АКБ. Конечно же, это не мера предосторожности против удара током, а защита электрооборудования автомобиля от вероятного короткого замыкания, которое может возникнуть при проведении ремонтных работ.
Иногда замену можно выполнить за 10-15 минут – например, если повреждены провода питающей цепи «АКБ-генератор». Если же нарушена целостность проводки в салоне, есть проблемы с заземлением, короткое замыкание в цепи бортового компьютера, то работы отнимут гораздо больше времени. И главное здесь – не ошибиться, поскольку неправильное подключение проводов (например, при нарушении полярности) может вызвать короткое замыкание, повреждение дорогостоящего электрооборудования и даже возгорание. При отсутствии опыта в электротехнике и электромонтажных работах лучше обратиться в специализированный сервис за услугами автоэлектрика-профессионала.
Источник Источник Источник http://extxe.com/16156/tehnicheskoe-obsluzhivanie-jelektrooborudovanija-avtomobilja/
Источник http://studopedia.ru/2_12412_to-i-tekushchiy-remont-elektrooborudovaniya.html
Источник Источник http://ddcar.ru/blog/elektrika/kak-otremontirovat-elektroprovodku-avtomobilya